Machines
High-precision mechanical processing with multi-spindle machines
Microtecnica Trevisana SRL has an assorted and latest generation machine park: multi-spindle lathes and transfer machines for the production of customized high precision CNC machining parts in brass and automatic steel.
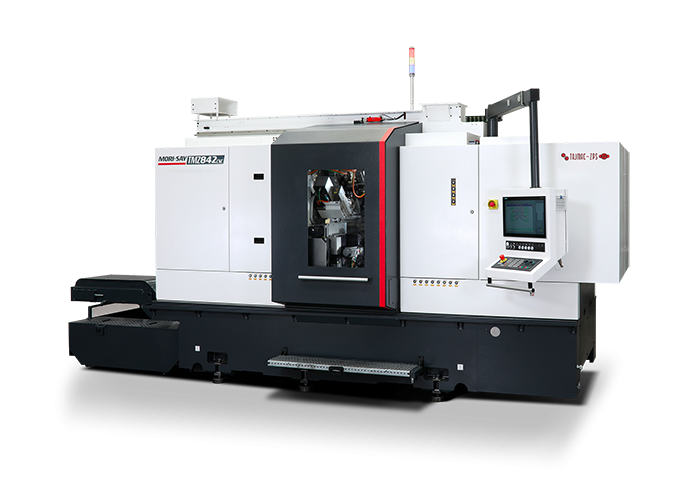
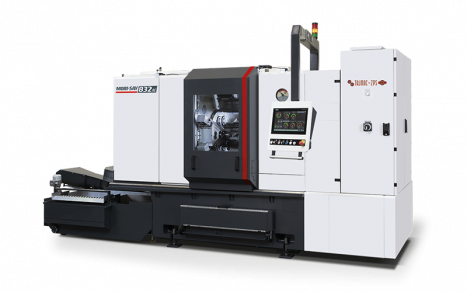
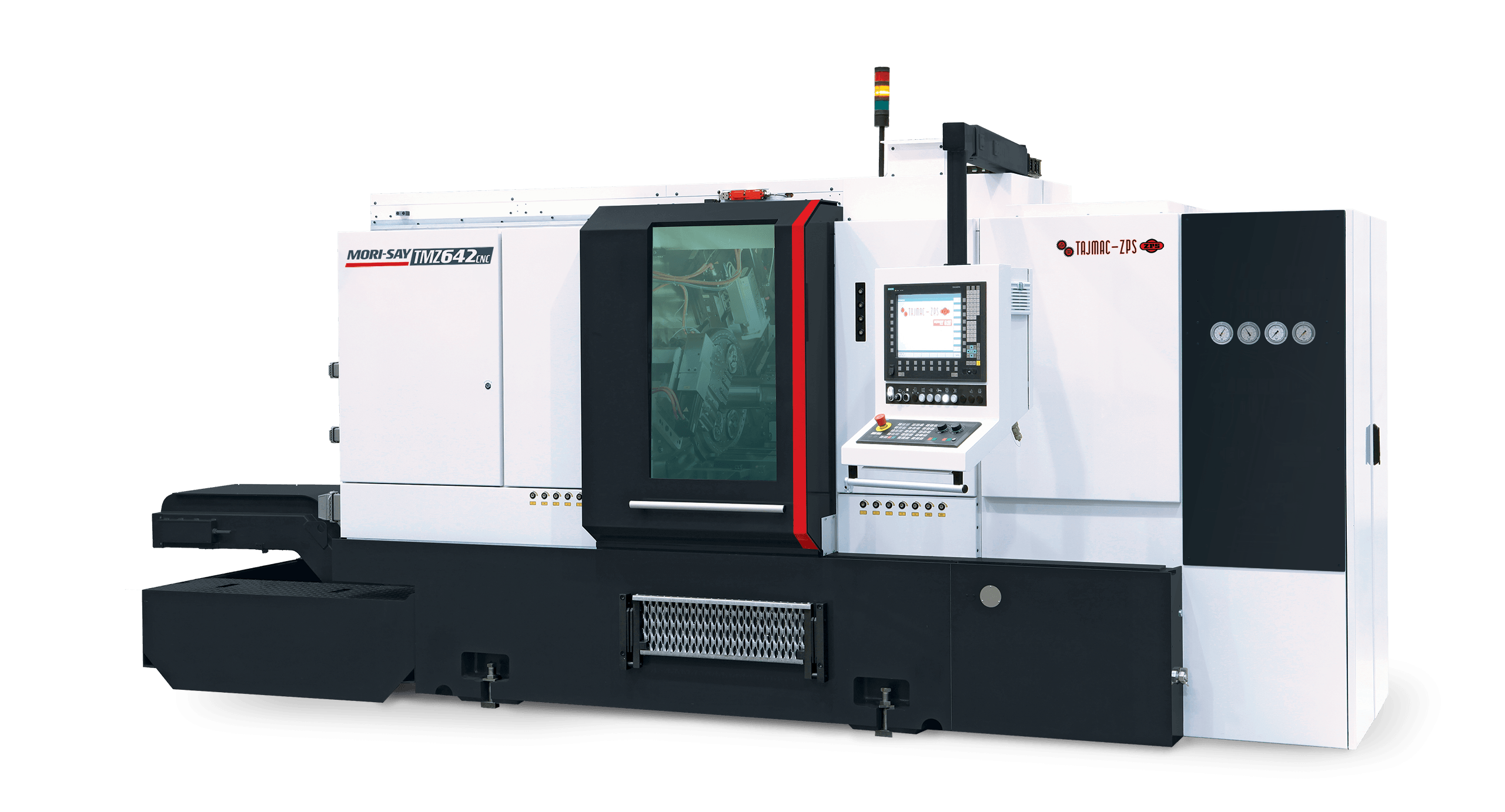
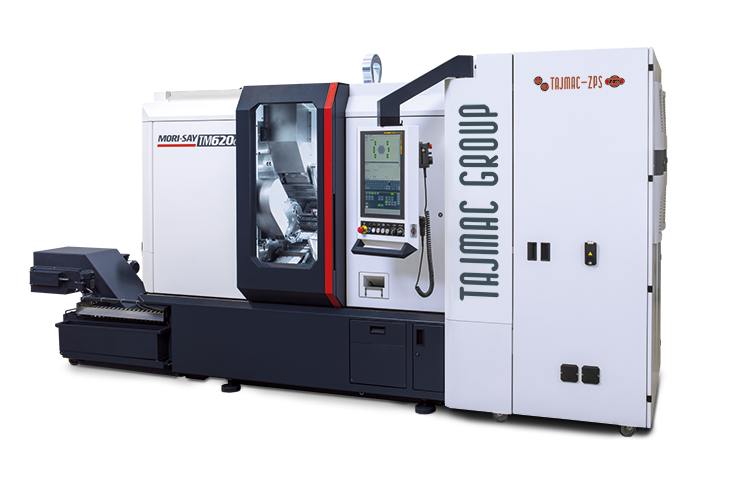
Machines
The company’s machinery park consists of 45 multi-spindle lathes with numerically controlled movement slides and pick-up and spindle stop devices, as well as a line of 7 bar TRANSFER machines to increase production capacity and meet customer needs.
Our capacity list includes: TAJMAC (MORI-SAY 8/32, 8/42, 6/20, 6/25, 6/42), TAJMAC CNC (TMZ 6/42), SCHÜTTE (AG-20) e GNUTTI TRANSFER MACHINE G444.
To provide a complete service to our customers, we use state-of-the-art equipment, including:
- 2 IFP (Innovative Fluid Processing) washing machines equipped with ultrasonic technology using modified alcohols for extremely efficient cleaning of components;
- 1 automated department with 20 machines for assembling o-rings and other components;
- 1 automatic line for creating custom blister packaging
- 1 automatic line for composing and labeling boxes;
- 1 RÖSLER vibro-finishing system for surface finishing of small components;
- 2 REA (Robotic End-of-Arm-Tooling) robotic inspection cells used for quality control of products.
Instrumentation for measurement and control.
The following machinery and measuring instruments are used during the control of our production processes:
N. 1 VICIVISION optical measuring machine;
N. 1 PROFILOMETER;
N. 2 DELTA VISIONE automatic sorting machines;
N. 2 KEYENCE measuring machines;
N. 2 SMARTSCOPE FLASH OGP (optical machine);
N. 2 RUGOSIMETERS.
Centesimal digital CALIPERS with data output;
Digital micrometres (0-25 and 25-50) with data output;
Calibrated PLUG GAUGES for measuring holes and threads;
Digital comparators for length measurement;
Digital and analog comparators for measuring grooves.
All measurements taken are recorded during the production phase, and a final inspection certificate is issued before the piece is shipped